В 1971 году бывшие сотрудники компании Boeing, инженеры Джим Леа (Jim Lea), Нил Андерсон (Neil Anderson) и Джон Барроуз (John Burroughs), использовали пресс-форму для сэндвичей, чтобы соединить кусок поролона с двумя фрагментами воздухонепроницаемой ткани. В результате получился маленький прототип самонадувающегося коврика. Это событие стоит у истоков одной из самых авторитетных компаний в мире outdoor — Therm-a-Rest.
Серийный выпуск самонадувающихся ковриков начался в 1972 году в Сиэтле, США. Во главу угла компании был поставлен принцип высокого качества выпускаемой продукции — только так можно было побороть скепсис туристов относительно кажущейся «ненадёжности» самонадувающихся ковриков. С первых лет своей работы Therm-a-Rest предоставляет на них пожизненную гарантию. Недаром первым слоганом компании стала фраза «For the rest of your life» — «До конца твоей жизни».
Всё производство Therm-a-Rest сосредоточено на двух предприятиях в США и Ирландии. И сегодня мы познакомимся с процессом производства самонадувающихся ковриков на фабрике в Сиэтле.
Первый этап — поступление сырья на фабрику и создание заготовок будущих ковриков. Огромные блоки полиуретановой пены прибывают на фабрику от проверенного поставщика. Далее они нарезаются на отдельные листы на специальном станке. Поверхность резчика представляет собой аэростол. Блок пены сначала беспрепятственно скользит по воздушной подушке, а затем надёжно притягивается к столу за счёт откачивания воздуха. Затем пеноблок начинают катать вперёд-назад через горизонтальное лезвие. Оно срезает ровные листы, начиная сверху и опускаясь до самого низа пеноблока. На этом этапе задаётся толщина будущего коврика.
Фрагменты пены, оставшиеся после перфорации цельного листа, скапливаются под прессом. Затем воздухом их затягивает в большую трубу, по которой они попадают в огромные пластиковые пакеты. В дальнейшем их не будут выбрасывать, а используют в качестве набивки для подушек Therm-a-Rest.
Следующий большой этап в производстве самонадувающихся ковриков Therm-a-Rest — герметичное «запечатывание» заготовки из пены в оболочку из воздухо- и водонепроницаемых тканей. Это едва ли не самая ответственная часть всего процесса, ведь от того, насколько хорошо склеятся ткань и пена, зависит долговечность и надёжность коврика. Плохая склейка равна высокому риску образования грыж или травления воздуха через швы. Для оболочки самонадувающегося коврика используются различные ткани, отличающиеся составом, плотностью и обработкой, — всё зависит от назначения модели. В коврах серии Fast & Light ткань будет тоньше и легче, в серии Trek & Travel — более прочной и износостойкой, а в серии Camp & Comfort — ещё и тактильно мягкой для более комфортного сна.
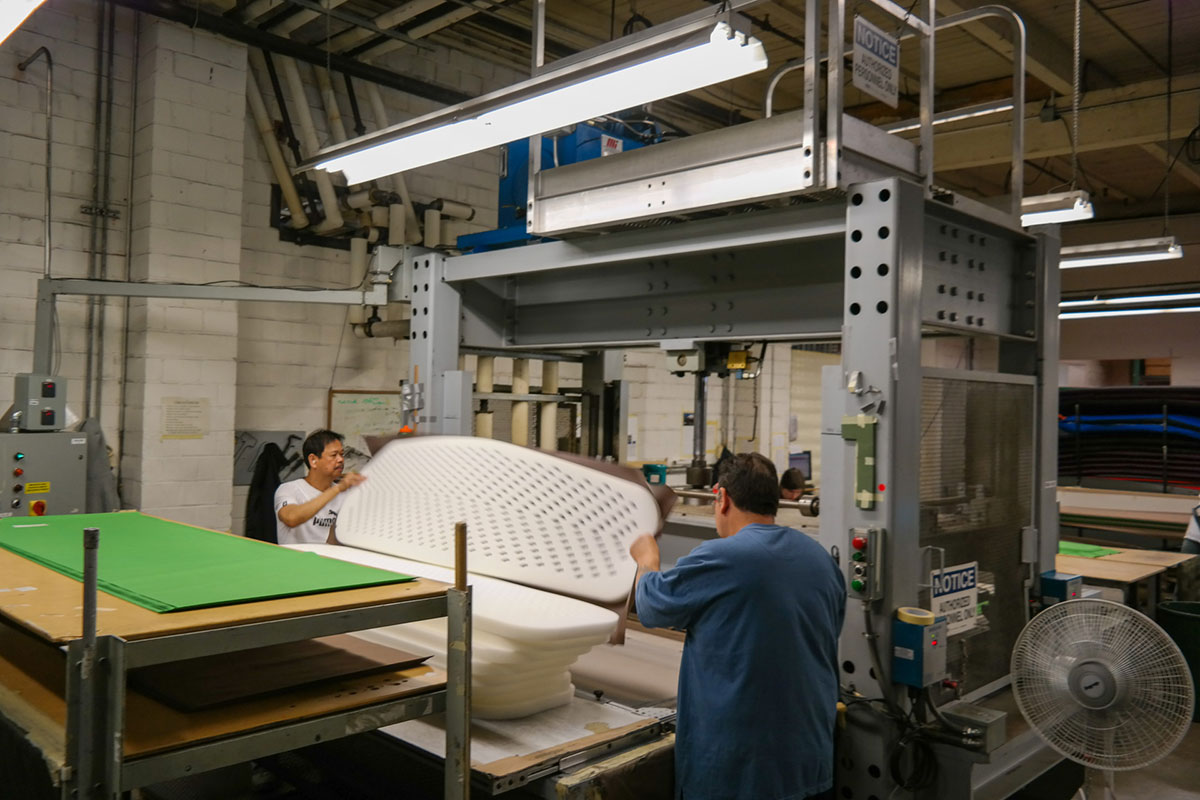
Работники на фото располагают заготовку из пены между верхним и нижним слоями ткани будущего коврика. Далее этот «бутерброд» отправляется в станок, который склеивает его воедино. Поверхность пресса нагрета горячим маслом. Прогревается вся поверхность коврика, при этом особое внимание уделяется шву по его периметру. Источник фото: gizmodo.com
Заключительный этап производства ковриков Therm-a-Rest — очень тщательная проверка качества изготовления, упаковка и отправка в магазины.
После того как коврик прошёл все тесты на контроль качества, его сжимают насколько возможно с помощью пресса. В нём матрасы выкладываются на гладкие деревянные панели, которые не способны как-либо повредить поверхность коврика.
А далее упакованные коврики отправляются на склады готовой продукции и оттуда в магазины. Например — в «Спорт-Марафон»!